Wprowadzenie
MPER, czyli Multi-Purpose Exploration Rover, to dotychczas najdłużej trwający projekt inżynieryjny i programistyczny SKN SpaceCoffee, rozpoczęty w 2023 roku. Jest to również pierwszy oryginaln i pełnoprawny projekt, nad którym nasze Koło rozpoczęło prace. Zapraszamy do zapoznania się ze szczegółowymi informacjami na temat łazika opracowanego przez SpaceCoffee.
Robotyczni posłańcy
Od momentu gdy pojawiliśmy się na tym świecie, ludzie starają się jak najlepiej poznać go i rządzące nim zasady. Jeszcze wczoraj odkrywaliśmy nowe wyspy i kontynenty, a dziś zrobotyzowani posłańcy odwiedzają obce planety i księżyce. Te bezzałogowe, autonomiczne pojazdy—łaziki—zostały zaprojektowane do eksploracji obcych ciał niebieskich i trudno dostępnych terenów. Ich główną misją jest badanie tych miejsc: zbieranie okazów, gromadzenie bezcennych danych o panujących tam warunkach. Badania te są znaczącym krokiem ku rozszerzaniu naszej wiedzy o przestrzeni kosmicznej i planetach, a także w badaniu możliwości kolonizacji kosmosu i tworzenia naukowych baz kosmicznych. Tak liczne wieści o wielu trwających i planowanych misjach z udziałem łazików zainspirowały nas do zbudowania własnego.
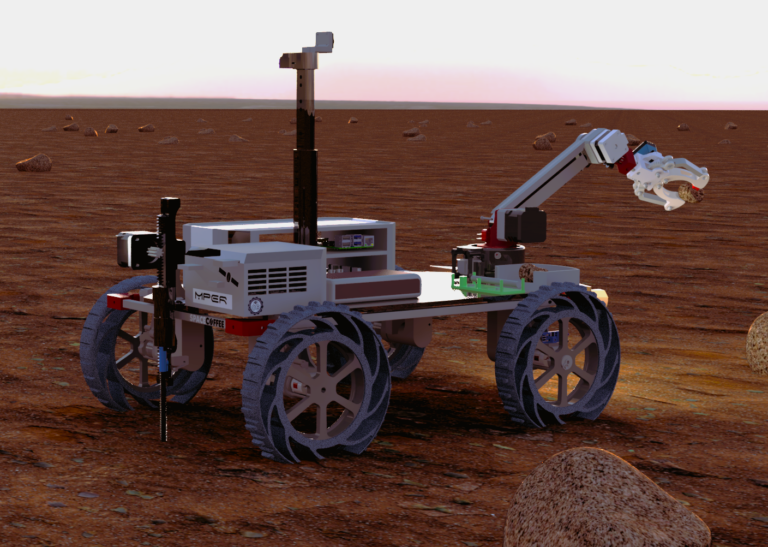
Cele i założenia projektu
Zaplanowany zestaw funkcji łazika
- Zdalne sterowanie zadaniami i półautonomiczne nawigowanie za pomocą interfejsu użytkownika stworzonego podczas projektu, komunikacja za pośrednictwem Wi-Fi 2,4 GHz/5 GHz.
- Możliwość precyzyjnej manipulacji, która będzie możliwa dzięki opracowanemu ramieniu robotycznemu z modułem manipulatora.
- Pobieranie próbek z i spod powierzchni dzięki w pełni rozwiniętemu, efektywnemu modułowi wiercenia i przechowywania; możliwość przechowania do 5 próbek.
- Realizacja celów badawczych—możliwa dzięki wdrożeniu czujników środowiskowych do badania składu gleby, atmosfery i wykrywania promieniowania, wraz z systemem ważenia pobranych próbek.
- Łazik jest wyposażony w trzy kamery: szerokokątną, noktowizyjną o średnim kącie widzenia i do rozpoznawania obiektów przy użyciu AI. Kamera szerokokątna może obracać się w osi pionowej lub poziomej za pomocą serwomotoru.
- Jazda po wzniesieniu o nachyleniu do 30 stopni.
- Zbudowany spersonalizowanie system LIDAR, który stanowi podstawę do autonomicznej nawigacji łazika.
- Zaimplementowany ma zostać algorytm planowania ścieżki, pozwalający łazikowi na autonomiczne poruszanie się po terenie z wykorzystaniem GNSS, znaczników wizualnych i czujników przeszkód.
- Wykorzystanie czujników poboru prądu, gromadzących dane diagnostyczne modułów łazika.
Projekt łazika zakładał opracowanie taniego w budowie i łatwego do powielenia rozwiązania konstrukcyjnego, co skłoniło nas do zaproponowania wymiarów: masa poniżej 18 kg i wymiary platformy 700x450x300 mm. Prostota naszego łazika pozwala na równoległą obsługę i kontrolę wielu mniejszych pojazdów tego typu, co zmniejsza ryzyko awarii pojedynczego robota, od którego zależy powodzenie całej misji, podczas bardziej złożonych zadań operacyjnych. Do tego, rozległy teren może być eksplorowany przez wiele mniejszych łazików. Koncepcja misji, o której myśleliśmy, obejmuje główny niemobilny lądownik—laboratorium naukowe, z flotą dziesiątek łazików i dronów różnych rozmiarów i funkcjonalności, przygotowujących i dostarczających tam próbki.
Moduły i ich implementacja
Podczas projektowania naszego pojazdu pod uwagę wzięto wszystkie elementy niezbędne do jego działania. Z tego powodu, komponenty zostały podzielone na następujące moduły i odpowiadające im systemy:
- Platforma jezdna—podwozie: skonstruowany napęd ma zapewnić dostosowanie łazika do nierównych i wymagających powierzchni planetarnych, dzięki napędowi na 4 koła z systemem pochłaniania wstrząsów, który zapewnia mu dodatkową zwinność ruchu w trudno dostępnych lub trudnych do nawigowania miejscach.
- Robotyczne ramię i manipulator z chwytakiem: komponent musi umożliwiać precyzyjną interakcję z otoczeniem; ramię manipulatora ma 4 stopnie swobody i pięć przegubów, w którym zastosowaliśmy zaprojektowaną kombinację 2 typów przekładni – przekładni stepped-planetary, w całości wydrukowanej z PETG. To zapewnia nam łatwość eksperymentowania z parametrami ramienia, dzięki czemu możemy określić najlepszy projekt jego konstrukcji. Łazik może zbierać materiały z otaczających go powierzchni i przenosić je na swoją platformę, która jest wyposażona w wagę do wstępnego określenia parametrów próbki.
- Całe ramię jest lekkie, ma 4DOF i wykorzystuje 3 silniki krokowe i 2 serwomechanizmy do precyzyjnej nawigacji ruchu. Jego maksymalny udźwig planowany jest na 1 kg.
- System przechowywania próbek: opracowaliśmy inteligentny system pojemników—pojedynczy czujnik siły dla przedniej komory i drugi pojedynczy czujnik z tyłu dla próbek z głębokich odwiertów. Czynność umieszczenia próbki jest rejestrowana, a waga obliczana na podstawie różnicy w całkowitej wadze modułu, z dokładnością +/- 0,5 g, przy użyciu pojedynczego czujnika wagowego. Pozwala to na przechowywanie wielu próbek bez użycia większej liczby czujników wagowych. Magazyn dla próbek z głębokich odwiertów cechuje się obrotowym systemem wymiany pojemników i ma również opcję sekwencyjnego ich opróżniania, przy użyciu pojedynczego serwomechanizmu do obracania przedziału. Przedni przedział ładunkowy nadaje się do przechowywania skał lub innych przedmiotów zebranych przez łazik, a także do składowania podstawowych narzędzi, które mogą być używane przez manipulator. Zawarty tam jest też czujnik promieniowania jonizującego, jako część modułu czujników środowiskowych (do badania atmosfery) oraz czujnik masy.
- System odwiertu: moduł odpowiedzialny za pobieranie próbek gleby. Obecna głębokość planowana dla zanurzenia wiertła wynosi do 20 cm pod powierzchnią. Najnowsza konstrukcja systemu obejmuje silnik krokowy przesuwający wózek po prowadnicy „V-slot”, z ogranicznikiem na górze. Moment obrotowy silnika krokowego jest zwiększany za pomocą naszej niestandardowej przekładni.
- Prowadnica jest podzielona na dwie części – stałą i ruchomą. Część stała zapewnia oparcie mechaniczne i działa jak łożysko liniowe, podczas gdy część ruchoma jest przymocowana do wózka i ściśle przylega do wiertła, umożliwiając próbkom gleby przemieszczanie się w górę, jak pokazano na schematach systemu odwiertu.
- System pobierania próbek: składa się z dwóch innych modułów: manipulatora i systemu odwiertu. Przedni przedział ładunkowy znajduje się w zasięgu ramienia robota. Po pobraniu, próbki mogą być transportowane i przechowywane w przygotowanych pojemnikach korzystając z manipulatora. Wymaga to uwzględnienia ich szczególnej kruchości i zapewnienia wcześniejszej sterylizacji pojemnika. Wiertło obraca się wzdłuż prowadnicy, umożliwiając przeniesienie próbki do góry w kierunku systemu przechowywania próbek.
- Komputer główny i komputery podsystemów: odpowiedzialne za koordynację pracy całego łazika. Przesyłanie informacji i komend pomiędzy podsystemami odbywa się poprzez magistrale SPI podłączone do głównego komputera łazika. Opracowaliśmy 3 odrębne płytki PCB dla głównych podsystemów: Chassis, Manipulator i Sampler, wszystkie trzy napędzane przez niezależny mikrokontroler (Arduino Nano), odbierający i wysyłający dane do głównego kontrolera (Raspberry Pi 5).
- Moduł czujników środowiskowych: służący do badania warunków środowiskowych panujących na planetach innych niż Ziemia. Jest zbiorem czujników przeznaczonych do zbierania danych o składzie i stanie atmosfery oraz gleby. W celu analizy czynników atmosferycznych skompletowaliśmy oparty na Arduino Nano system czujników ciśnienia, temperatury, wilgotności i CO₂.
- Dodatkowo nasz łazik wyposażony jest w czujnik promieniowania jonizującego, umieszczony obok przedniego przedziału ładunkowego. Może on być wykorzystywany do pomiaru promieniowania tła i burz słonecznych, a także do wykrywania radioaktywności obiektów odebranych przez łazik.
- Badanie czynników związanych z warunkami glebowymi będzie możliwe dzięki zastosowaniu sond wilgotności i temperatury.
- Wymienione powyżej czynniki są potrzebne do oceny elementów natury planety, oceny jej zamieszkiwalności i, na przykład, zdolności do hodowli roślin. Pomiary przygotowane podczas badania próbki są przesyłane z modułów sensorycznych poprzez magistralę UART do komputera głównego opartego na Raspberry Pi 5. Zanotowane wartości są następnie przesyłane do bazy naziemnej w celu prowadzenia dalszych badań. Ważnym dodatkiem w pracach jest czujnik promieniowania UV.
- Intuicyjny interfejs użytkownika: pełną kontrolę nad łazikiem można uzyskać w przeglądarce, z telemetrią i podglądem na żywo. Opracowujemy system wyznaczania trasy, w którym operator może dotknąć punktu w zasięgu wzroku łazika, a ten dojedzie do niego, omijając po drodze przeszkody. Interfejs użytkownika może być dostępny przez przeglądarkę na dowolnym komputerze PC lub urządzeniu mobilnym, umożliwiając intuicyjne sterowanie pojazdem.
- Zbudowany pod specjalne potrzeby system przypominający LIDAR: składający się z „wieżyczki” z czujnikiem laserowym o dwóch DOF, który może celować w dowolny obiekt i zwracać jego odległość od łazika.
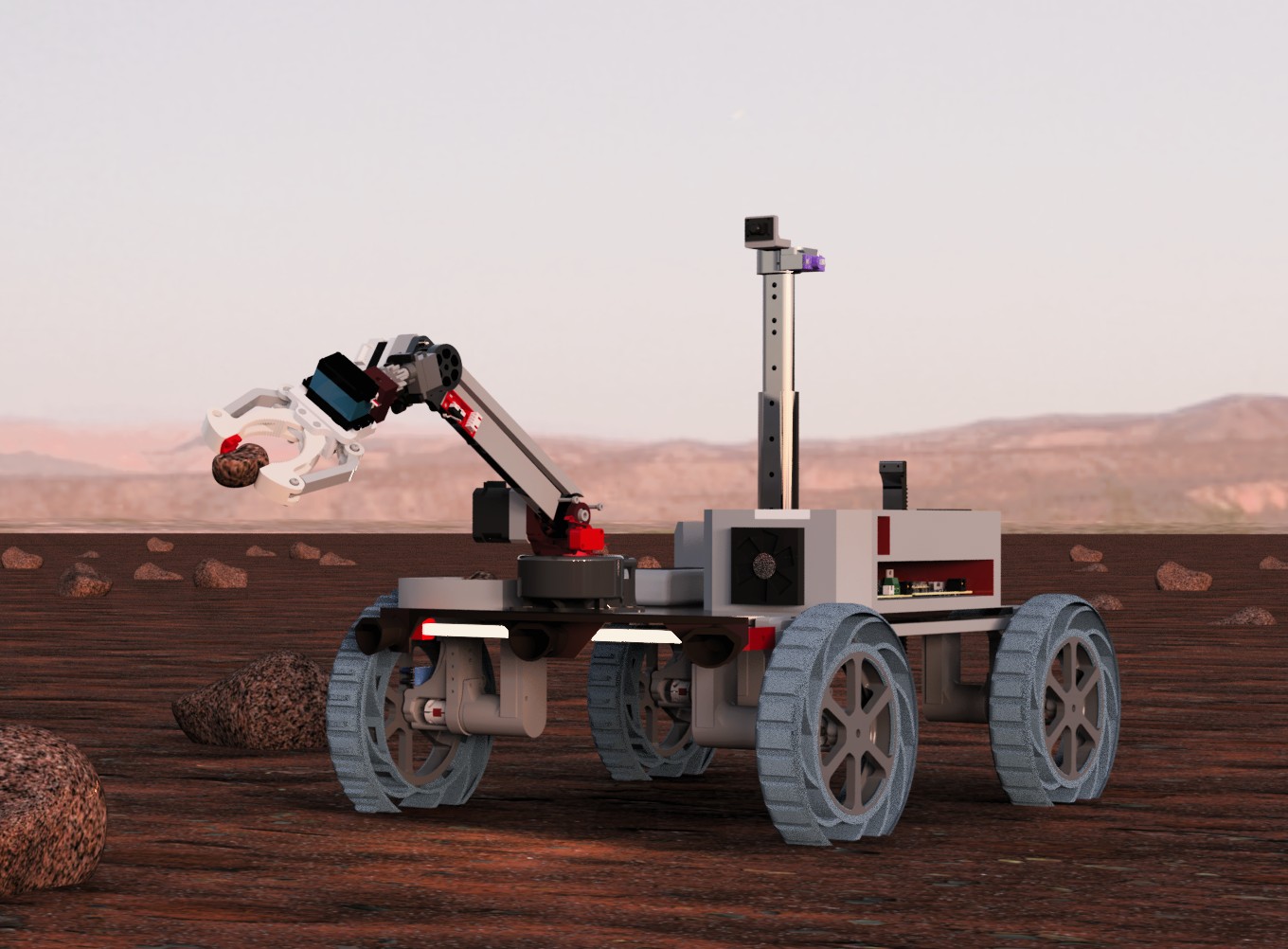
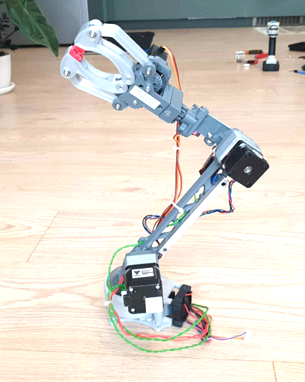
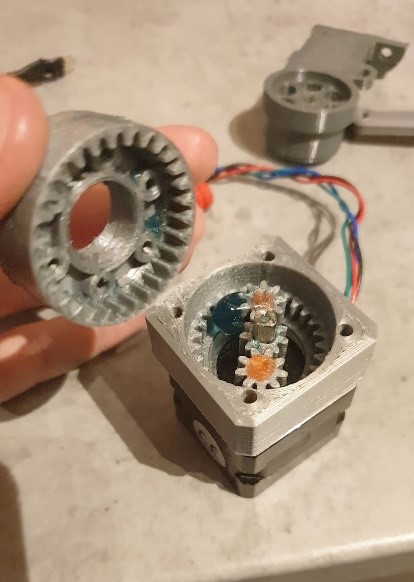
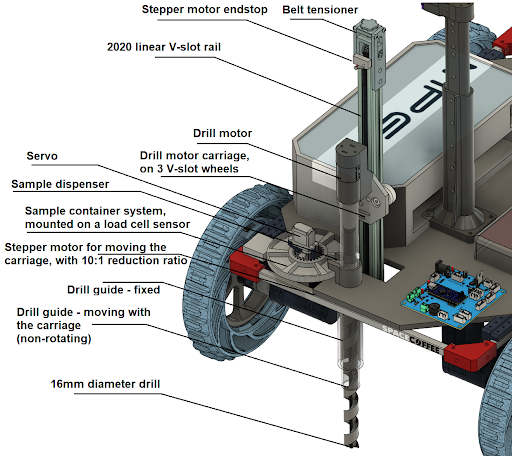
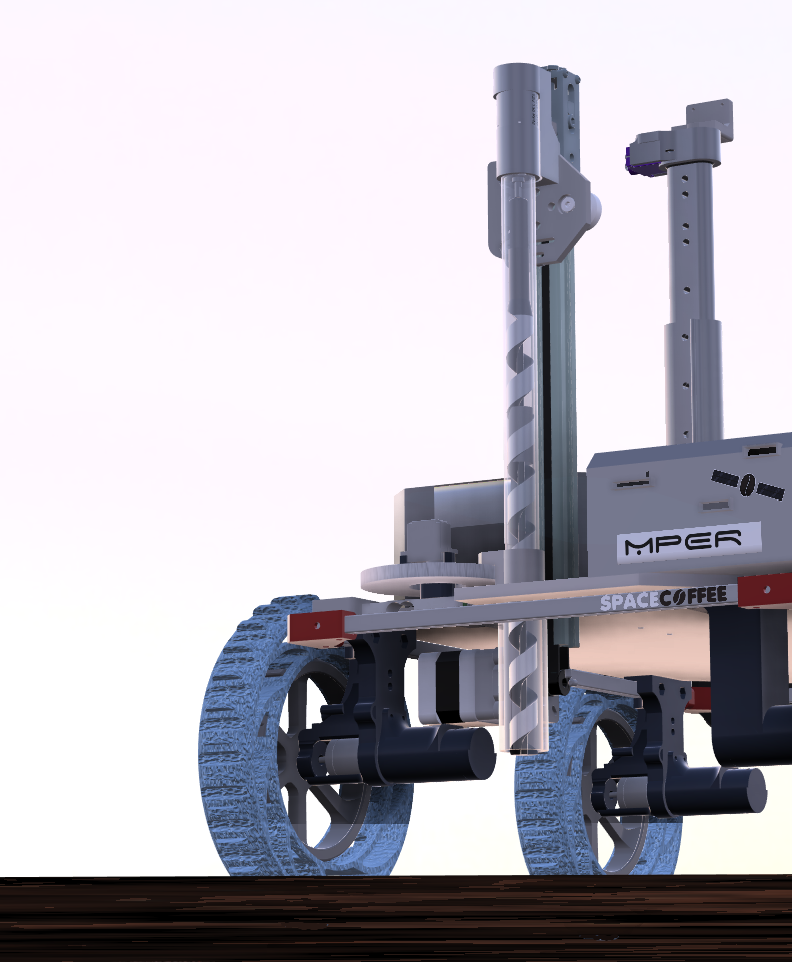
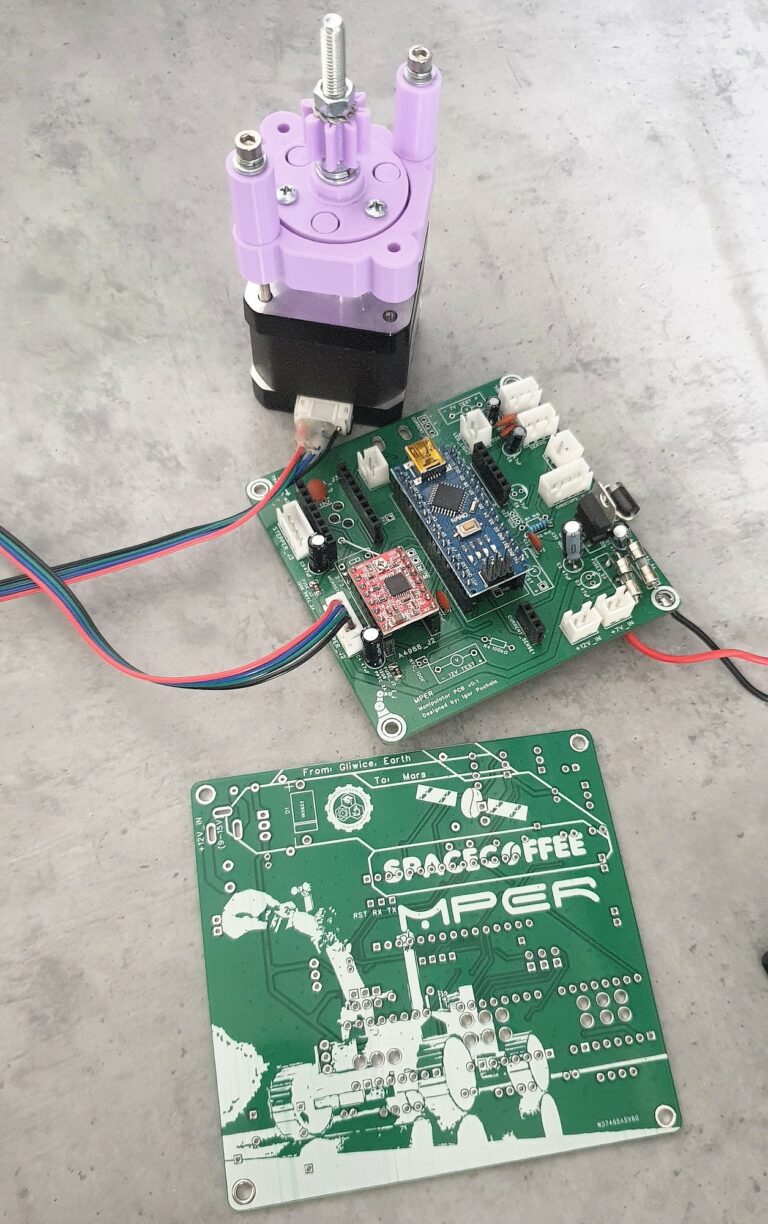
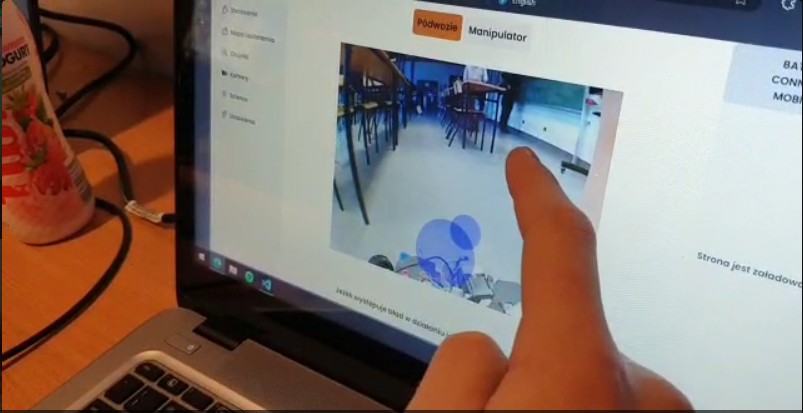
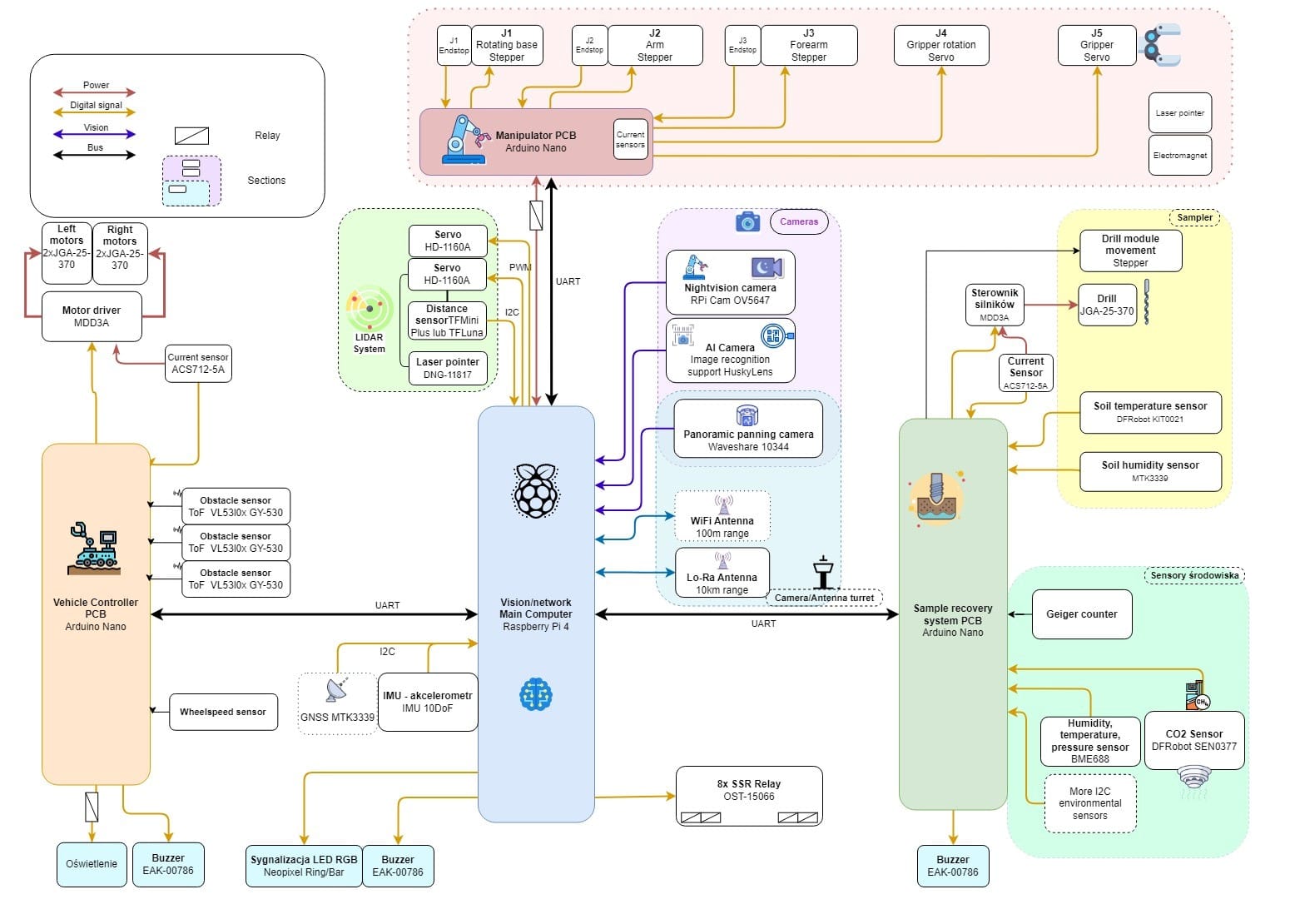
Rozwój: posty związane z projektem MPER
Sample collection and containment system for a compact planetary exploration rover
Tytuł: Sample collection and containment system for a compact planetary exploration rover Autorzy: Maja Rudnicka, Michał Lasak, Igor Puchała, Piotr Bartosz, Dominik Bereta, Dariusz Myszor Konferencja: International Students Scientific Conference TalentDetector2024_Summer Abstrakt: The purpose of this research is to develop an exploration rover to use in Earth and Martian-like environments, which requires the development of…
Rozwój projektu MPER (2023)
Uzyskane ulepszenia Podczas tegorocznych prac nad łazikiem wdrożyliśmy imponującą liczbę zaplanowanych funkcji i komponentów. Nasze prace koncentrowały się na: — Zakończeniu projektowania zintegrowanego układu na płytce PCB. — Modernizacji podwozia naszego łazika, w oparciu o wnioski wyciągnięte z testów poprzedniego modułu. Obecnie używane podwozie jest przeznaczone do budowy pełnowymiarowej konstrukcji. — Projektowaniu, produkcji elementów, instalacji…
MPER na Konferencji „Projekt Politechnika”
Zespół rozwoju łazika z naszego Koła zaprezentował MPER na konferencji projektów licealnych PBL, organizowanej przez Politechnikę Śląską. Zademonstrowali zarówno aktualny model łazika, jak i poster podsumowujący ich pracę nad projektem. Poster przygotowany na Konferencję MPER podczas prezentacji na Konferencji „Projekt Politechnika”
Przyszłe potencjalne zmiany
Główne dwa rozwiązania postrzegane jako przyszłe rozszerzenia łazika to: diagnostyka poboru prądu, do której planujemy wykorzystać 5 czujników poboru prądu—ich zastosowanie obejmuje pomiar sił chwytaka i przegubów manipulatora, a także wiertła w ruchu. Pozwala to również na diagnostykę układu napędowego i oszacowanie czasu pozostałego do rozładowania akumulatora. Drugim rozszerzeniem jest wykorzystanie paneli słonecznych jako części modułu zasilania. Możliwe jest zaprojektowanie składanego układu paneli słonecznych do ładowania ogniw, aby zachować mobilność i stabilność łazika, gdy nie jest ładowany.